RTLS for Manufacturing
Gain Real-Time Visibility & Maximize Efficiency
Reduce delays, improve visibility, and keep production moving with Locaxion’s RTLS for manufacturing. Track work-in-progress, locate equipment in real time, and automate key workflows across your facility. With live data at your fingertips, you can make faster decisions and get more value out of your assets, all with a system that fits directly into your existing operations.
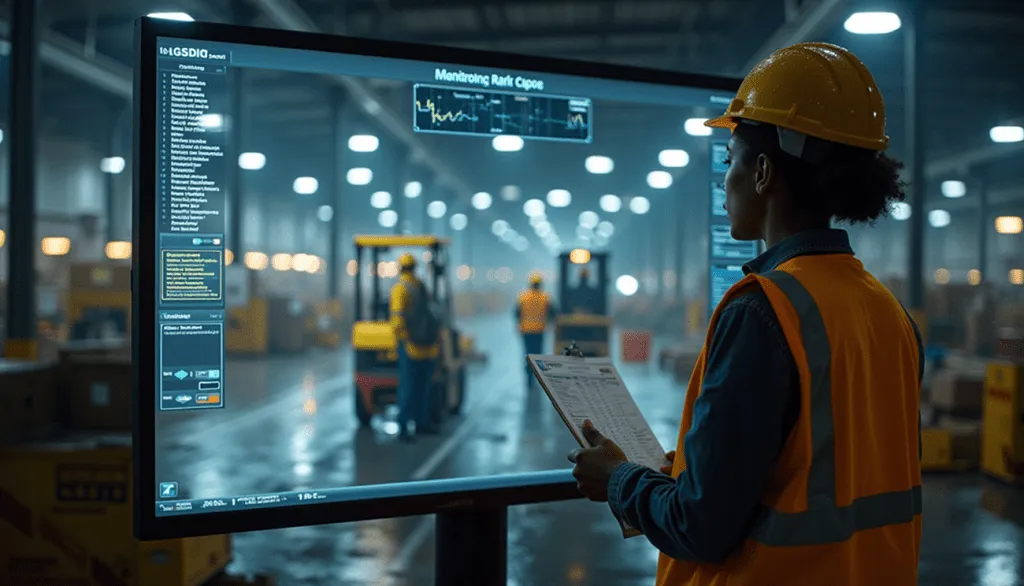
Key Benefits of Indoor Employee Tracking System
Reduce Workplace Incidents with Real-Time Hazard Monitoring
Minimize costly accidents by continuously tracking worker movements with sub-meter accuracy. RTLS instantly alerts when employees enter hazardous areas, preventing unauthorized access and ensuring compliance with OSHA 1910.146 for confined space monitoring. This proactive approach reduces liability risks and lowers incident-related expenses.
Automate Compliance & Eliminate Safety Violations
RTLS automates PPE enforcement and ensures only certified workers access high-risk zones, preventing regulatory fines. By supporting ISO 45001 and OSHA 1910.132, businesses can reduce the administrative burden of manual compliance tracking while strengthening workplace safety policies.
Accelerate Emergency Response & Minimize Downtime
RTLS enhances evacuation efficiency by tracking personnel in real time, ensuring full accountability during emergencies. Complying with NFPA 101, it enables faster rescues, reducing potential injury claims and downtime while improving business continuity.
Key Performance Statistics
~34%
Reduction | 1.4 fewer incidents
Fewer Workplace Incidents
~75%
Increase | +6 near-miss reports per quarter
More Near-Miss Reports
~40%
Improvement | 4.5 minutes faster evacuation
Faster Emergency Response
~25%
Increase | +18 percentage points in PPE compliance
Higher Safety Compliance
~25%
Reduction | 4 fewer lost days per 100 employees/year
Fewer Lost Workdays
How RTLS Enhances Manufacturing Process Optimization
Dynamic Task Sequencing for Adaptive Production
Optimize workflows with real-time task adjustments RTLS dynamically reorganizes production tasks based on real-time locations of raw materials, workers, and tools—ensuring continuous flow and preventing downtime.
- Example: Machines prepare for the next production step as materials move along the line. If delays occur, RTLS automatically reschedules tasks to keep operations running.
Real-Time Work-in-Progress (WIP) Tracking
Gain end-to-end production visibility
Track every component at each stage of production, identify delays instantly, and take corrective actions in real time.
- Example: In automotive manufacturing, RTLS ensures every part reaches the right assembly station on time, reducing bottlenecks and optimizing throughput.
Automated Assembly Line Synchronization
Seamlessly coordinate materials, tools, and assembly lines
RTLS ensures just-in-time (JIT) material arrival, minimizing misalignment and errors in high-speed production lines.
- Example: Car doors arrive at the exact moment they are needed in chassis assembly, preventing mismatches and delays.
Automated Tool Operation & Verification
Enhance precision with intelligent tool activation
RTLS-enabled tools activate and configure settings automatically when placed over the correct workpiece, reducing human error.
- Example: In electronics manufacturing, torque wrenches auto-adjust for exact torque settings when positioned correctly, ensuring accuracy.
Error-Proofing & Quality Control Integration
Detect and prevent defects in real time
RTLS integrates with quality control systems to monitor deviations and enforce standard operating procedures (SOPs).
- Example: In aerospace, RTLS ensures the correct tools, parts, and personnel are at each workstation—automatically flagging anomalies for immediate correction.
Human-Robot Collaboration for Safe & Efficient Operations
Enable seamless coordination between workers and machines RTLS tracks human and robotic movements to prevent collisions and enhance productivity.
- Example: On an electronics assembly line, robotic arms dynamically adjust speed and paths to avoid interfering with nearby human inspectors.
Automated Production Line Reconfiguration
Quickly adapt to new production requirements
RTLS enables modular production setups, allowing seamless reconfiguration for new models or demand shifts.
- Example: In aerospace, RTLS tracks movable workstations, enabling rapid layout changes without interrupting workflows.
Predictive Bottleneck Analysis
Prevent downtime before it happens
RTLS analyzes real-time production data to identify potential bottlenecks and optimize resource allocation.
- Example: In a packaging facility, RTLS detects accumulating pallets and alerts managers to adjust staffing or equipment usage proactively.
Component Traceability for Compliance & Quality Assurance
Ensure full traceability from raw materials to finished products
RTLS provides real-time tracking for regulatory compliance, recalls, and quality audits.
- Example: In pharmaceutical manufacturing, RTLS maintains a live digital record of each batch’s journey, ensuring compliance with stringent industry regulations.
Autonomous Material Handling & Delivery
Optimize material flow with intelligent automation :
RTLS guides autonomous vehicles and AGVs (Automated Guided Vehicles) for precise, real-time material transport.
- Example: In automotive plants, RTLS-powered AGVs deliver engine components just in time to prevent production slowdowns.
Why Locaxion is the Right Partner for Your RTLS Journey?
100+ Location Intelligence projects
With expertise across over 100 successful projects, we deliver proven solutions for manufacturing and warehousing industries.
15+ years of experience in RTLS
Our team brings extensive expertise in RTLS, digital twins, and smart factory consulting alongside leading industry partners.
Strong Network of Top RTLS
We collaborate with industry-leading RTLS and digital twin providers to create tailored, client-specific solutions.
Why You Need RTLS for Manufacturing Efficiency & Process Optimization
Real-Time Location & Movement Tracking – Gain Unmatched Visibility
Seamless Integration with MES, ERP & IoT Systems – Enable Intelligent Automation
Scalable & Adaptable RTLS Infrastructure – Future-Proof Your Operations
Turn Movement into Metrics with RTLS-Powered Process Improvement
Locaxion provides manufacturing process optimization services built around real-time location data, giving teams the visibility they need to make informed decisions on the fly.
By capturing precise movement and usage patterns of assets, materials, and personnel, our RTLS solutions create a foundation for smarter planning and faster response to changes on the floor.
Whether you’re looking to optimize manufacturing process flow, reduce idle time, or better manage resource allocation, real-time location technology gives you the data to act with confidence.
These insights support measurable manufacturing process improvement, helping reduce waste, improve throughput, and shorten production cycles, without overhauling your existing infrastructure.
Explore Real-Life Use Cases, Guides, and Insights on RTLS for Manufacturing
If you’re new to the world of manufacturing process automation, welcome. You’re stepping…
24 Jun 2025
Lone workers face unique risks every day, from environmental hazards to sudden medical…
31 Mar 2025
In today’s fast-paced industrial environments, ensuring worker safety and optimizing operational efficiency are…
31 Mar 2025
RTLS for Manufacturing: Automate Workflows, Reduce Delays
Ready to eliminate production bottlenecks, enhance real-time visibility, and automate workflows? Locaxion’s RTLS process automation solutions streamline manufacturing operations, improve productivity, and maximize ROI through advanced workflow optimization.
Frequently Asked Questions
How long does it take to see results from manufacturing process optimization?
The timeline depends on project complexity and implementation scope. However, initial improvements are typically noticeable within the first few months. We set clear goals, track key milestones, and ensure measurable progress throughout the process.
Can small and mid-sized manufacturers benefit from process optimization?
Absolutely. Our solutions are scalable and adaptable, making them suitable for small and mid-sized manufacturers. Regardless of company size, optimizing workflows leads to reduced costs, improved efficiency, and higher output.
What are common challenges companies face when implementing process optimization?
Challenges may include resistance to change, system integration issues, data accuracy concerns, and specialized training needs. Successful implementation requires strategic planning, clear stakeholder buy-in, and expert support—all of which we provide.
How do you ensure that new processes remain sustainable long-term?
Sustainability is key. We provide ongoing support through maintenance, training, and continuous improvement programs, ensuring that process optimizations become part of your long-term operational success.
How can automation technologies enhance manufacturing process optimization?
Automation technologies, such as real-time work-in-progress (WIP) tracking, error-proofing, and robotic-human coordination, improve efficiency by eliminating bottlenecks, enhancing quality control, and enabling predictive analysis.
What tools or technologies assist in streamlining manufacturing processes?
Real-Time Location Systems (RTLS) play a critical role in optimizing processes by automating workflows, ensuring real-time tracking, and improving production accuracy. Other tools, including MES and ERP integrations, further enhance efficiency.
How does implementing optimization strategies improve efficiency?
Optimization strategies such as dynamic task sequencing, real-time WIP tracking, and automated assembly line synchronization drive efficiency. These approaches reduce downtime, improve productivity, and create a seamless production environment.